Die Ostschweiz steht für eine lange Tradition in der Textilindustrie. Einzelne Unternehmen produzieren bis heute und behaupten sich mit innovativen Produkten auf dem Weltmarkt. Zu ihnen gehört die Heberlein AG in Wattwil (SG). Die 90 Mitarbeiterinnen und Mitarbeiter stellen Spezialteile für Maschinen zur Garnherstellung her. Eine dieser Komponenten wird gegenwärtig so weiterentwickelt, dass ein energieintensiver Prozessschritt der Garnherstellung künftig mit 30 Prozent weniger Energie auskommen könnte. Das weltweite Einsparpotenzial ist erheblich.
Die Heberlein AG wurde im Jahr 1835 als Garnfärberei gegründet. Von Mitte der 1930er Jahre an stellte die Toggenburger Fabrik die Viscose-Kunstseide Helanca her. Ab 1950 verlagerte sich die Tätigkeit von der Garnherstellung auf den Bau von Textilmaschinen bzw. deren Komponenten. Solche Spezialkomponenten sind – neben Keramikteilen u.a. für die Medizin – heute noch eine Exklusivität des Wattwiler Unternehmens. Sie kommen in der Herstellung von synthetischen Garnen weltweit zum Einsatz. Ein Schwerpunkt ist dabei Asien, denn dort haben die meisten Heberlein-Kunden ihre Produktionsstätten.
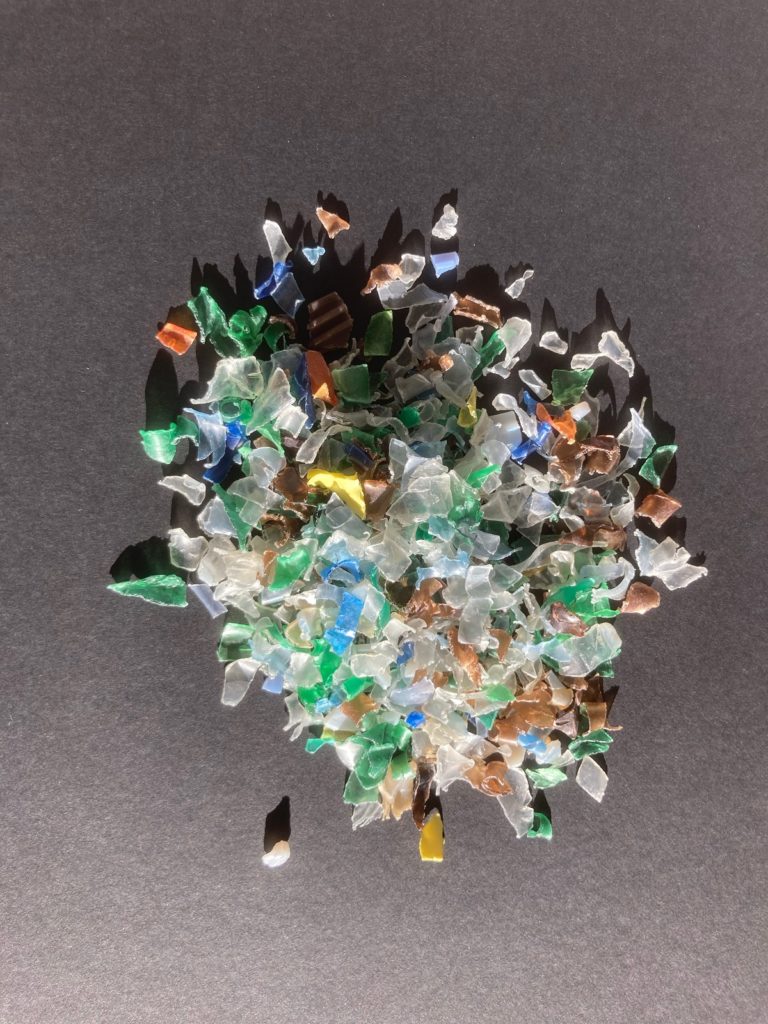
Druckluft verbindet die Kunststofffasern
Synthetische Garne gehören zur Klasse der Chemiefasern und bestehen aus anwendungsspezifisch aufbereiteten Kunststoffen. Ausgangsstoff der Garnproduktion in einer Chemiefaserspinnerei ist ein Kunststoffgranulat. Die Herstellung des Garns läuft – vereinfacht dargestellt – in folgenden Schritten ab: Das Granulat wird erhitzt, dann mittels Spinndüsen in feine Kunststofffasern (Filamente) umgeformt und abgekühlt. Mehrere Dutzend oder sogar mehrere Hundert solcher Fasern werden zu einem Garn gebündelt und nach einer Weiterbearbeitung in der sogenannten Streckzone schliesslich auf eine Spule gewickelt. In dieser Form vertreibt die Spinnerei die Garne an ihre Kunden.
Damit aus den Filamenten ein kompaktes Garn entsteht, ist vor dem Aufwickeln ein zusätzlicher Prozessschritt erforderlich: Hierbei werden die Filamente mithilfe eines dünnen Druckluftstroms verwirbelt. Das hat zur Folge, dass sich die einzelnen Fasern zu einem kompakten Garn verbinden.
Fachleute bezeichnen den Vorgang als «Knotenbildung» beziehungsweise als «Fadenschluss». Die Knotenbildung ist unabdingbar, damit das Garn später mit hoher Geschwindigkeit und ohne Abriss weiterverarbeitet werden kann.
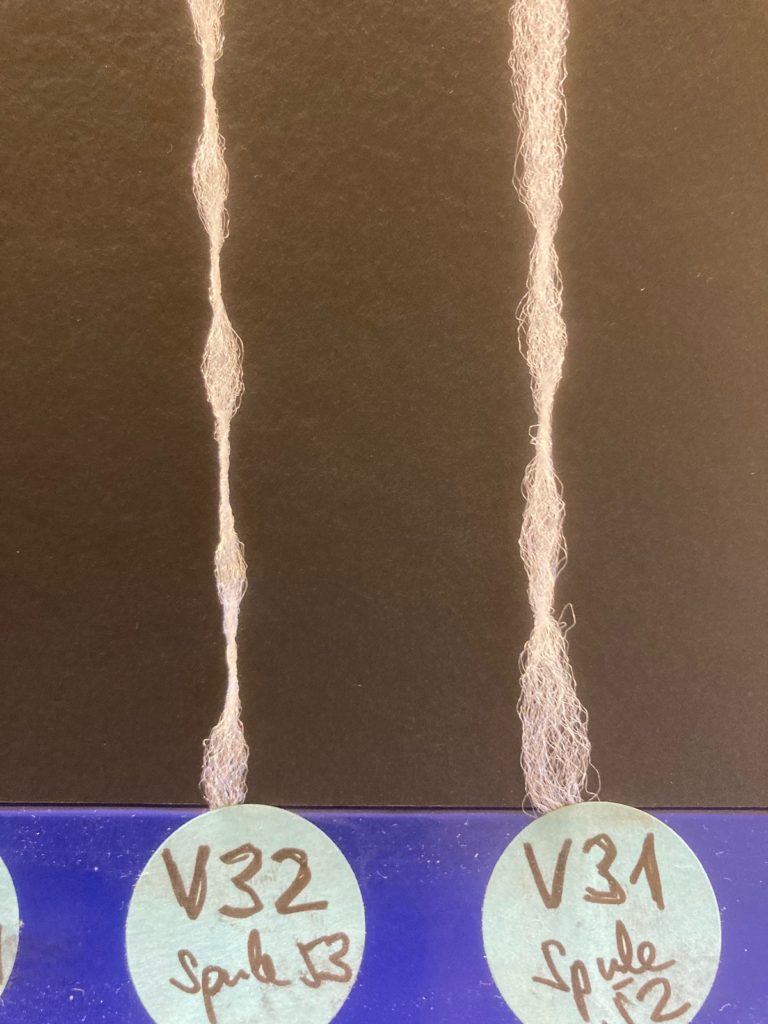
Energieintensiver Prozessschritt
Der Verwirbelungsprozess wird seit Jahrzehnten zur Herstellung von hochwertigem Garn eingesetzt. Die dafür notwendigen Verwirbelungsdüsen stammen von der Heberlein AG in Wattwil oder von einem der insgesamt rund zehn Hersteller weltweit, die über das entsprechende Knowhow verfügen. «Der Verwirbelungsprozess ist sehr energieintensiv, er ist in einer Spinnerei für 15 bis 30 Prozent des Energieverbrauchs verantwortlich», sagt Patrick Buchmüller, Technikchef der Heberlein AG.
Vor diesem Hintergrund startete die Firma ein Entwicklungsprojekt mit dem Ziel, den Verwirbelungsprozess mit einem neuen Verfahren energieeffizienter zu gestalten. Heberlein spannte dafür mit dem Engineering-Büro «streamwise» in Männedorf (ZH) zusammen. In einem vom BFE unterstützten Vorprojekt wurde eine neue Verwirbelungstechnologie mit Einsatz von Fluidoszillatoren konzipiert und im Labormassstab erfolgreich getestet.
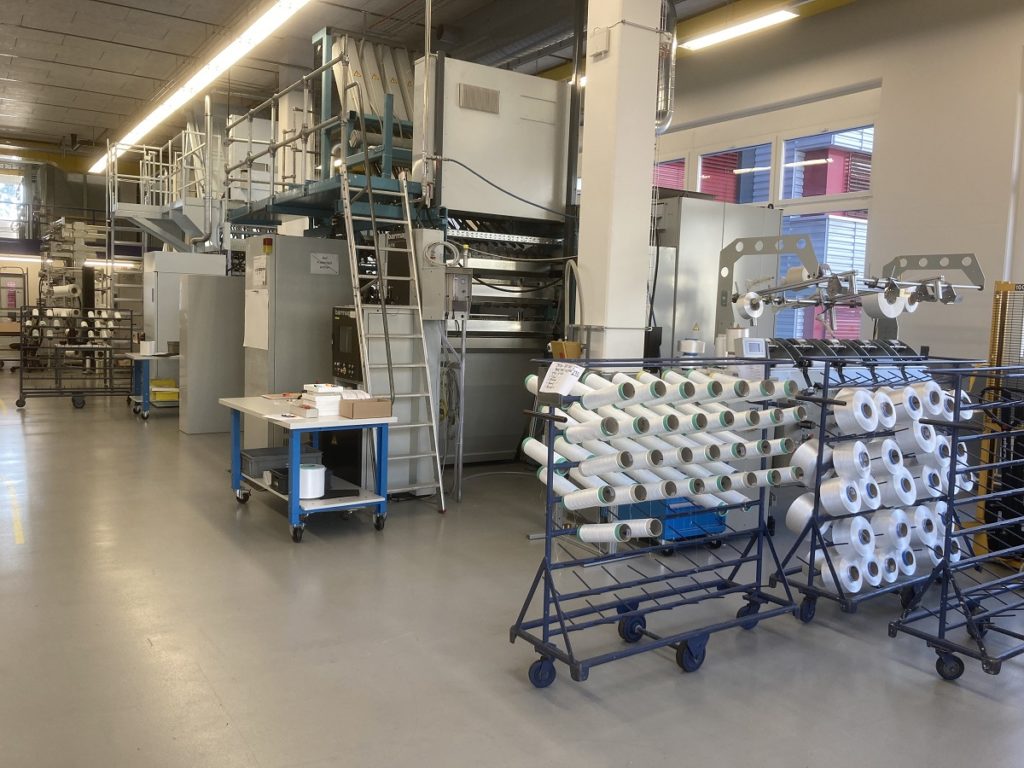
30 Prozent weniger Energie
In einem mehrjährigen Folgeprojekt – finanziert aus dem Pilot- und Demonstrationsprogramm des BFE – wurde der Einsatz der Technologie nun im industriellen Massstab erforscht. Dabei wurden verschiedene Varianten einer Oszillator-basierten Verwirbelungsdüse (vergleiche Textbox) konstruiert und anschliessend im Heberlein-Labor in Wattwil, aber auch im Institut für Textiltechnik der RWTH Aachen und auf einer industriellen Spinnereimaschine mehreren Testprogrammen unterzogen.
Nachdem das Projekt Anfang 2022 mit dem Schlussbericht abgeschlossen wurde, zieht Dr. Benjamin Rembold vom Engineering- Büro «streamwise» eine positive Bilanz: «Die entwickelten Verwirbelungsdüsen mit Oszillator funktionieren fluiddynamisch hervorragend bei moderaten Prozessgeschwindigkeiten und bei feinen bis mittleren Garnen. Für hohe Prozessgeschwindigkeiten und groben Garne müssen weitere Tests gefahren und allenfalls weitere Optimierungsschritte vorgenommen werden.» Im Laborversuch konnten dank der neuartigen Düse 30 Prozent Energie gespart werden.
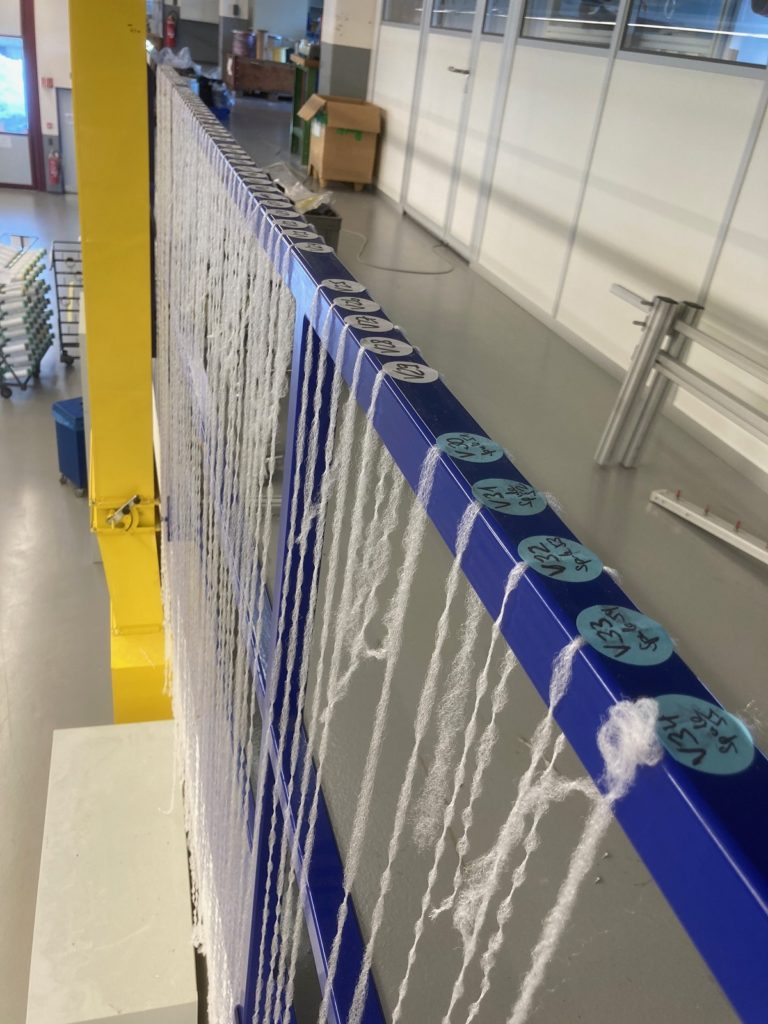
Mehrere Jahre bis zur Marktreife
Die Ergebnisse des Projekts haben die Verantwortlichen von Heberlein darin bestärkt, die Entwicklung der Verwirbelungsdüse bis zur Marktreife voranzutreiben. «Mit Blick auf ein serienreifes Produkt muss die Verwirbelungsdüse verkleinert werden. Auch muss die neue Komponente so ausgelegt werden, dass sie in bestehende wie neue Maschinen eingebaut und für verschiedene Garntypen genutzt werden kann», sagt Heberlein-Projektmanager Andreas Brunner. Bis zu einem marktreifen Produkt rechnet Brunner mit einer mehrjährigen Entwicklungszeit. Als Einsatzgebiet für die neuen Verwirbelungsdüsen steht die Produktion von Teppichgarnen und technischen Garnen (für Sicherheitsgurte, Airbags, Lkw-Blachen und vieles mehr) im Vordergrund, während deren Einsatz im Bereich der Textilgarne (Kleiderproduktion) wegen der hohen Fadendichte in den dort eingesetzten Spinnmaschinen schwierig ist. In den beiden Einsatzgebieten ergibt sich ein erhebliches Einsparpotenzial, wie die folgende Überschlagsrechnung zeigt: Eine Chemiefaserspinnerei, deren Maschinen beispielsweise 640 Garne herstellen, verbraucht rund 36’000 Kubikmeter Druckluft pro Stunde, zu deren Produktion Kompressoren rund 3 600 Kilowattstunden Strom benötigen. Diese Fabrik braucht also für die Verwirbelung der Garne in der Stunde etwa so viel Strom wie ein durchschnittlicher Vier-Personen-Haushalt pro Jahr. Einer Expertenschätzung zufolge liessen sich bei einem weltweiten Einsatz der neuen Verwirbelungstechnologie jährlich 360 Gigawattstunden Strom sparen, was der Jahresproduktion eines grösseren Wasserkraftwerks entspricht.
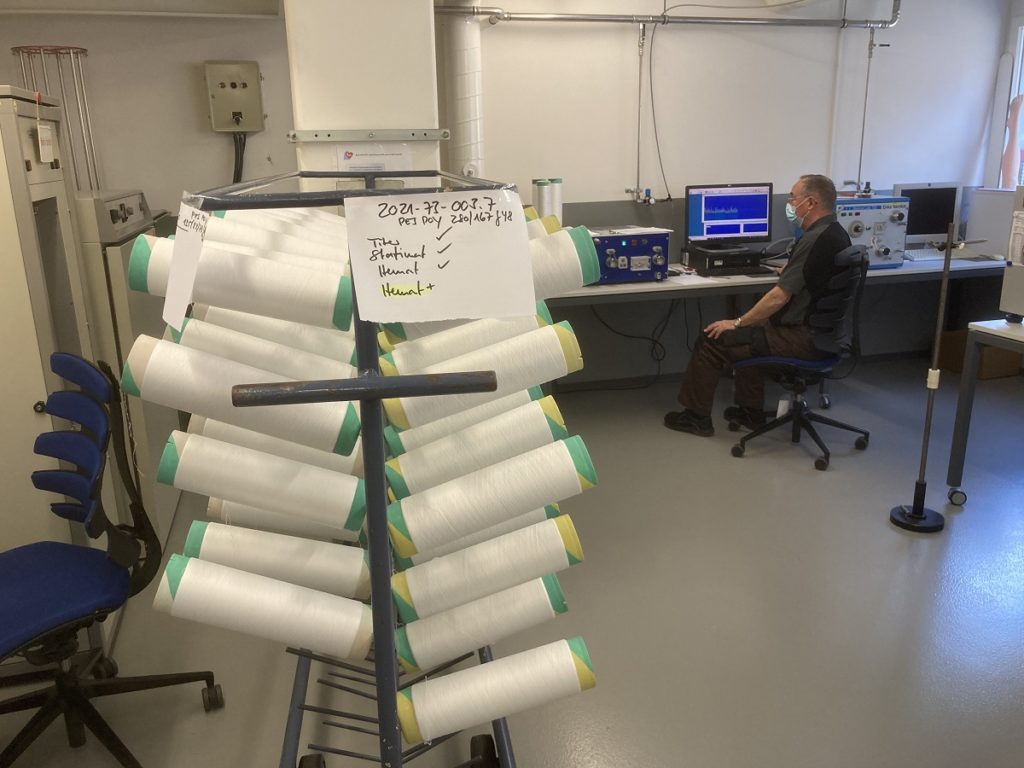
Hinweis
Der Schlussbericht zum Projekt ‹Oszillator-basierte Verwirbelungsdüse: Industrielle Machbarkeit› ist abrufbar unter: www.aramis.admin.ch/Texte/?ProjectID=41462
Auskünfte zu dem P + D-Projekt erteilen Dr. Carina Alles (carina.alles@bfe.admin.ch), Leiterin des BFE-Forschungsprogramms Industrielle Prozesse, und Dr. Men Wirz (men.wirz@bfe.admin.ch), verantwortlich für das Pilot- und Demonstrationsprogramm des BFE.
Weitere Fachbeiträge über Forschungs-, Pilot-, Demonstrations- und Leuchtturmprojekte im Bereich Industrielle Prozesse finden Sie unter www.bfe.admin.ch/ec-prozesse.